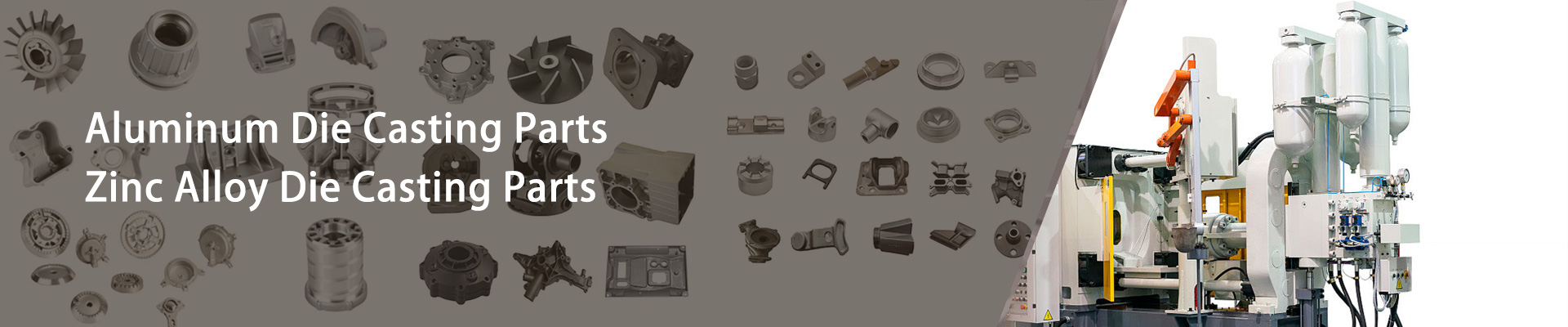
2024 European Aluminum Die Casting Award" Winning Aluminum Alloy Die Castings(Part2)
2024-01-25 11:00
Valve Body WAG100148L100
Description:
Design, casting, and molding requirements, including assembly components:
No damage or dents in the sealing area. No flattening in the external threaded casting.
Design, Casting, and Molding Requirements:
Exceptional casting quality, threads comply with specifications.
Why Adopt Die Casting Production?
Reduces machining, cost savings. Previously a machined part.
Why This Part Won the European Die Casting Award?
Innovative solution, prevents flattening during external threaded casting. High-quality characteristics of the sealing surface. Manufactured using aluminum thermal chamber process.
Technical Data:
Length: 18 mm
Width: 16 mm
Height: 16 mm
Weight: 3.5 grams
Alloy: EN-AC 46000 AL 226 D
Lightweight Vehicle Wheel Hub Electric Motor E-Coil
Description:
Design, casting, and molding requirements, including assembly components: High requirements for the surface and microstructure of thread-like, complex, and thin-walled components (few pores and voids).
Design, Casting, and Molding Requirements:
Innovative mold separation and precision mold design required. Vacuum degassing must be used to meet high structural requirements.
Why Adopt Die Casting Technology?
Through collaboration with Ifam Fraunhofer in Bremen, the copper coil used for lightweight vehicle wheel hub motors was replaced with die-cast aluminum coils using the Al-DG process. This innovation opens up new applications, significantly reducing weight (aluminum coils are over 50% lighter than copper coils, currently reducing material by over 30%). Additionally, aluminum processing saves resources due to its low melting temperature.
Why This Component Won the European Die Casting Award?
Aluminum replaces copper, reducing reliance on raw materials.
Aluminum coil weight is about 50% lighter than copper coils.
Material cost for aluminum coils is about 60% lower than wound copper coils.
Optimized use of space for cast aluminum coils, performance data almost comparable to wound copper coils.
Lower carbon footprint for aluminum coils due to lower processing temperature compared to wound copper coils.
Better heat dissipation for aluminum coils compared to wound copper coils.
Technical Data:
Length: 65 mm
Width: 25 mm
Height: 11 mm
Weight: 15 grams
Alloy: Rotor Aluminum
Fisker Ocean Rear Guide Rail
Description:
Design, casting, and molding requirements, including assembly components: The aluminum die-cast "rear guide rail" is a highly stressed and safety-critical structural component in the vehicle body. It is also part of the rear axle housing, separating the wet and dry areas. The rear guide rail mainly withstands dynamic stress, must meet strict stiffness requirements, and requires necessary deformation capability for residual maneuverability in case of a collision. This component significantly reduces the scope of machining by slightly rotating the design direction.
Design, Casting, and Molding Requirements:
Due to the large size of the component, especially the geometric complexity of its length and wheel arch, the rear guide rail faces challenges in thermal deformation. To meet stringent elongation at break target requirements, a method combining low-volume spraying and high vacuum degassing is employed, minimizing residual moisture in the mold and optimizing the heat treatment process.
Why Adopt Die Casting Process?
As the rear guide rail is installed in electric vehicles, sustainability and lightweight considerations are essential. The rear guide rail can replace many independent formed metal sheet components, connectors, and longitudinal components in the overall design, providing a resource-saving and weight-optimized solution.
Why This Part Won the European Die Casting Award?
Developed a reliable ultra-long flow path manufacturing process.
Rivet die-casting, with low mold residual moisture, high elongation at break, and excellent casting quality.
Despite the challenging straightening process due to the large size and high stiffness of the component, it still meets strict tolerance requirements.
Reduced machining for the casting, achieving a lean production process.
As part of the development, various functions/connectors of steel connecting components are integrated into the casting, reducing assembly scope.
Technical Data:
Length: 1282 mm
Width: 407 mm
Height: 645 mm
Weight: 10425 grams
Alloy: AlSi10MnMg
Get the latest price? We will reply as soon as possible (within 12 hours)