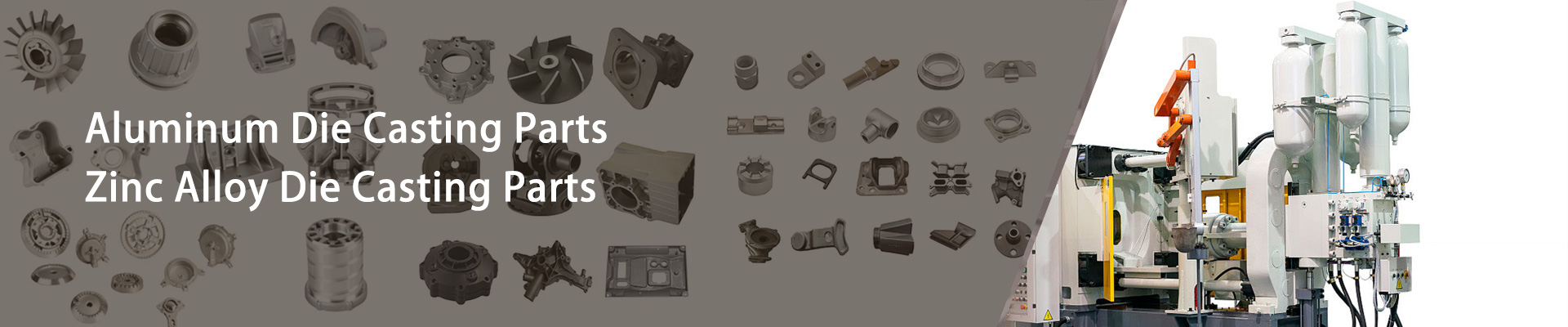
Aluminum Alloy Die Casting Standard
2023-09-13 02:30
1. Aluminum alloy GB/T 15115-941
Table 24-1 Chemical Composition and Mechanical Properties of Die-Cast Aluminum Alloys
No | Alloy Name | Alloy Code | Chemical composition % | Mechanical properties (not less than) | ||||||||||||
Silicon | Copper | Manganese | Magnesium | Iron | Nickel | Titanium | Zinc | Lead | Tin | Aluminum | Tensile strength | Elongation | Brinell hardness | |||
1 | YZA1Sil 2 | YL102 | 10.0 13.0 | ≤ 0.6 | ≤ 0.6 | ≤ 0.5 | ≤ 1.2 | ≤ 0.3 | remaining | |||||||
220 | 2 | 60 | ||||||||||||||
2 | YZAlSi10Mg | YL104 | 8.0 10.5 | ≤ 0.3 | 0.2 0.5 | 0.17 0.30 | ≤ 1.0 | ≤ 0.3 | ≤ 0.05 | ≤ 0.01 | remaining | 220 | 2 | 70 | ||
3 | YZAlSil2Cu 2 | YL108 | 11.0 13.0 | 1.0 2.0 | 0.3 0.9 | 0.4 1.0 | ≤ 1.0 | ≤ 0.05 | ≤ 0.3 | ≤ 0.05 | ≤ 0.01 | remaining | 240 | 1 | 90 | |
4 | YZAlSi9Cu 4 | YL112 | 7.5 9.5 | 3.0 4.0 | ≤ 0.5 | ≤ 0.3 | ≤ 1.2 | ≤ 0.5 | ≤ 1.2 | ≤ 0.1 | ≤ 0.1 | remaining | 240 | 1 | 85 | |
5 | YZAlSillCu 3 | YL113 | 9.6 12.0 | 1.5 3.5 | ≤ 0.5 | ≤ 0.3 | ≤ 1.2 | ≤ 0.5 | ≤ 1.0 | ≤ 0.1 | ≤ 0.1 | remaining | 230 | 1 | 80 | |
6YZAlSi17Cu5Mg | YL117 | 16.0 18.0 | 4.0 5.0 | ≤ 0.5 | 0.45 0.65 | ≤ 1.2 | ≤ 0.1 | ≤ 0.1 | ≤ 1.2 | remaining | 220 | <1 | ||||
7 | YZAlMg5Sil | YL302 | 0.8 1.3 | ≤ 0.1 | 0.1 0.4 | 4.5 5.5 | ≤ 1.2 | ≤ 0.2 | ≤ 0.2 | remaining | 220 | 2 | 70 |
2. Aluminum alloy die casting GB/T 15114-94
1 subject content and scope of application
This standard specifies the aluminum alloy die casting technical requirements, quality assurance, test methods, and inspection rules and delivery conditions.
This standard applies to aluminum alloy die castings.
2 Citation standard
GB 1182 Shape and position tolerance code and its standards
GB 2828 Batch-by-batch inspection count sampling procedures and sampling table (applicable to the inspection of successive batches)
GB 2829 Weekly inspection count sampling procedure and sampling table (applicable to the inspection of the stability of the production process)
GB 6060.1 Surface roughness comparison block Casting surface
GB 6060.4 Surface roughness comparison block Polished surfaces
GB 6060.5 Comparison of surface roughness of sample blocks of polished (blasted), sandblasted surfaces
GB 6414 Casting dimensional tolerances
GB/T 11350 Casting machining allowance
GB/T 15115 Die-casting aluminum alloy
3. Technical requirements
3.1 Chemical composition.
The chemical composition of the alloy shall comply with the provisions of GB/T 15115.
3.2 Mechanical properties.
3.2.1 When using a die-casting specimen test, its mechanical properties should be consistent with the provisions of GB/T 15115.
3.2.2 When using the die casting body test, its designated parts of the mechanical properties of the sample cut shall not be less than 75% of the single casting specimen, if there are special requirements, that can be agreed upon by the supply and demand sides.
3.3 Die casting size.
3.3.1 Die casting geometry and dimensions should be consistent with the provisions of the casting drawings.
3.3.2 Die casting size tolerance should be in accordance with the provisions of GB 6414, there are special provisions and requirements, that shall be specified in the drawing.
3.3.3 Die castings have shape and position tolerance requirements, and the labeling method is according to the provisions of GB 1182.
3.3.4 Die casting dimensional tolerances do not include casting slope, the surface is not machined: inclusive surface to the small end of the reference, the inclusive surface to the large end of the reference; to be machined surface: inclusive surface to the large end of the reference, the inclusive surface to the small end of the reference, there are special provisions and requirements, shall be indicated on the drawing.
3.4 Die castings need to be machined, and the machining allowance is in accordance with the provisions of GB/T11350. If there are special provisions and requirements, the machining allowance shall be indicated on the drawing.
3.5 Surface quality
3.5.1 The surface roughness of the castings shall comply with the provisions of GB 6060.1.
3.5.2 The castings are not allowed to have cracks, undercast, loose, bubbles or any penetrating defects
3.5.3 The castings are allowed to have defects such as abrasions, depressions, missing flesh, and mesh burrs, but the degree and quantity of the defects should be
The supply and demand sides agree with the standard.
3.5.4 Casting of the gate, fringe, overflow mouth, skin, top bar traces, etc. should be cleaned up, but allowed to leave traces of
3.5.5 If the drawing has no special provisions, about the die-casting process part of the setup, such as the top bar position, the location of the parting line of the position of the gate and the overflow port position, etc. by the production plant to stipulate their own; Otherwise, drawings should be indicated or agreed by the supply and demand.
3.5.6 die-casting parts need special processing. If special processing of the surface, such as polishing, shot peening, chromium plating, coating, anodizing, chemical oxidation, etc. shall be indicated on the drawing or agreed upon by the supply and demand sides.
3.6 Internal quality.
3.6.1 die casting if it can meet the requirements of its use, the die casting essential defects not as the basis for scrapping
3.6.2 die casting pneumatic sealing, hydraulic sealing, heat treatment, high-temperature coating, internal defects (porosity, porosity, cold segregation, inclusions) and the standard does not list the project requirements, which can be agreed upon by the supply and demand sides.
3.6.3 In does not affect the use of die casting conditions, when the demand side consents, the supply side can be on the die casting immersion and repair (such as welding, deformation correction, etc.) processing.
4. Quality assurance
4.1 When the supply and demand sides of the contract or agreement, the supply side of the contract is stipulated in all the tests or inspections responsible. When the contract or agreement does not provide, the demand side agreement, the supply side can use its own suitable means of implementation of the standard test and requirements. The demand side has the right to the standard of any test and inspection project inspection, its quality assurance standards should be based on the agreement between the supply and demand sides.
4.2 According to the characteristics of die-casting production, the provisions of a test batch refer to each die-casting equipment in normal operation under the circumstances of a shift of production, equipment, chemical composition, casting, and operation of any significant changes in continuity shall be considered as a new batch start.
The supplier of each batch of die castings should be randomly or statistically sampling inspection, to determine whether to comply with all the technical requirements and the contract or casting drawings of the provisions of the requirements, inspection results should be recorded
Get the latest price? We will reply as soon as possible (within 12 hours)